Workwear is having a moment
Everyday uniforms that people wear for their jobs — be it a pair of vintage checkered chef’s pants or a protective utility jumpsuit — are now being reimagined and made both more comfortable and fashionable.
Well-fitted workwear is one of the most important assets for a company that requires its employees to wear uniforms. It’s a visible way to convey a brand’s image, values, goals, and at the same time it represents an indispensable utility and means of protection for its people.
While there’s been a lot of debate around the feasibility of uniforms in some sectors, for others – like public service or military service – workwear is a necessity beyond debate. It is both a vitally protective garment and also represents a great source of pride for the serviceman who wears it.
A well-fitted uniform also goes a long way to convey trust, quality, and experience. And as companies have come to reconceptualize workwear for people who need not only practical but also stylish and perfect fit clothing for actual work, it is no wonder more and more uniform manufacturers and distributors are turning to technology to satisfy these needs.
The Challenge: Measuring for a perfect fit
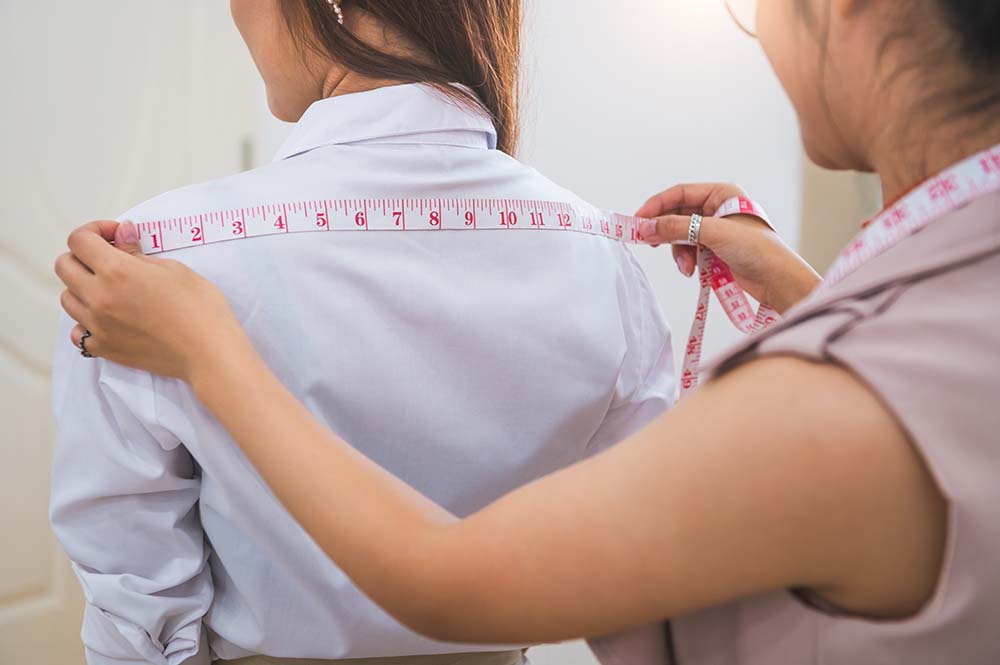
The current manual process for manufacturers and distributors of uniforms involves people and measuring tapes. For those who have leaned into technology, large and expensive scanning hardware is also an option. Either option drains resources and is time-consuming. Further, we as humans lose and gain weight which means that data is hard and expensive to update (assuming someone has even created a database of body measurements for their employees).
And the bigger the company, the bigger the collateral damage.
As brands and businesses grow, so does the distance tailors need to travel to measure employees, or vice versa, which puts a financial strain on the company in both travel expenses and lost productivity due to travel time.
The average manual body measuring procedure takes approximately 5-20 minutes. Meanwhile ordering uniforms in bulk – when an in-person measurement is required – automatically necessitates a one-by-one approach all destined to be time-consuming and wasteful.
And if to speed up the process, with long travel times, pressure to arrive quickly, and an overwhelming number of people to measure, tailors are stressed, tired, and prone to making mistakes. While ill-fitting, uncomfortable, too-tight uniforms may seem inconsequential to a layperson, professionals know that it does have serious implications and may pose safety hazards.
Besides, if the workwear or protective clothing appears to be ill-fitting because of the poorly taken measurements or a change of size – gaining or losing weight – it is usually up to the employee to bare the financial burden to have the item tailored to fit properly.
Another issue is the sheer number of people that large companies have to measure. Depending on the number of workers to be measured, manufacturers have to supply their own trained employees to take the measurements. So, imagine measuring 18,000 pilots for American Airlines, 70,000 annually-recruited soldiers, or 1,900,000 employees of the largest fast-food chain all over the world. The number of specialists needed to manually serve all these people is immense.
While it’s obvious that measuring for a uniform with a tape measure is an expensive in-person task draining tons of time, finance, and human resources, advances in technology have created an opportunity to digitize this process with mobile body scanning.
The shortest distance between two points is a straight line.
And the shortest distance between a tailor and a measured person is mobile body measuring software.
Saving Precious Time
Recent advances in AI-powered technologies such as computer vision and deep learning have enabled next-gen mobile body measuring solutions which focus on bringing significant efficiency to the uniform manufacturing supply chain. They revolutionize traditional practices by optimizing three interconnected aspects of the measuring process: people, time and money.
Cutting Unnecessary Expenses
The time you spend measuring customer’s employees is significantly reduced with mobile body scanners. For example, to fully measure a person with 3DLOOK mobile body measuring software takes less than a minute. On average, a professional tailor spends this time for one single measurement, so do the math. And the bigger the scale, the more time is saved – allowing businesses to optimize people resources and allocate money towards growth.
Leveraging the Data
For manufacturers or suppliers, sending staff long distances to manually measure customer’s employees is costly. The travel itself – plane tickets, lodging, and food – adds up. Mobile body scanning software allows anyone to measure themselves anywhere, alleviating the need to complicate schedules and move people around. The implications to global workforces are obvious.
The benefits of digitizing the measuring process have implications beyond saving time and resources. The data that this software computes allows manufacturers and distributors to focus on a body-centered design approach to use this data to optimize the product development, pattern making and grading process. The significance of understanding body data towards inventory forecasting, management, and planning is massive.
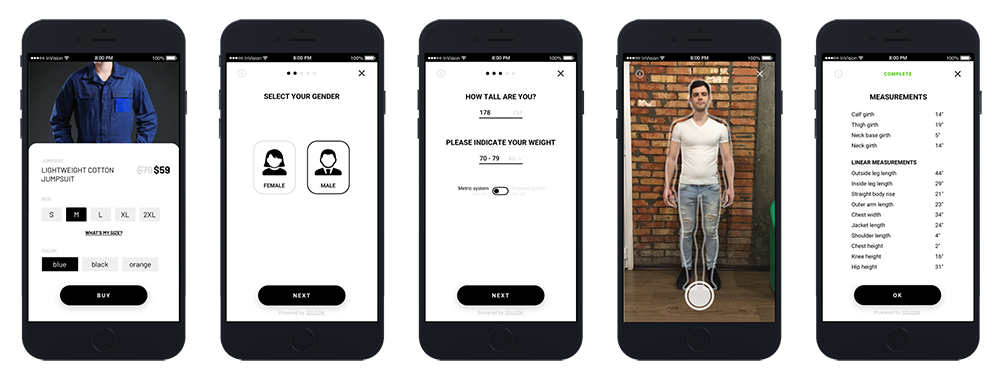
The global workwear market is huge – it was valued at $28.3 billion in 2018 – and for good reason. According to the Labor Department, there are about 3 million nurses and 2.5 million cooks, in the US alone. And a lot of them are young people who are used to buying everything online.
Following the transformation occurring in fashion apparel, the uniform segment is following suite and disruptive millennial founded uniform companies catering directly to the consumer are tapped to lead the next wave of disruption. Sellers Commerce predicts that even though uniform manufacturing will continue to be carried out on a contract basis, in the next couple of years the industry will be focused on e-commerce and new delivery methods.
The reason for this is pretty simple. From the consumer’s perspective, the idea of spending time traveling to a police, postal or fire gear store to be fitted and tailored is a huge waste of personal time. People want to buy their uniforms the same way they buy everything else – by pointing and clicking and having the items in their sizes delivered directly to their homes. Many hospitals are already allowing employees to buy scrubs from online uniform providers such as Lands’ End or Figs.
And as mobile devices have long come to play a major role in shopping – with more consumers completing their purchases via smartphones than computers – it is crucial for uniform suppliers to adapt their business model to get ahead. This is where mobile body scanning software comes in particularly handy as it puts the measuring device right into employee’s hand thus providing convenience, portability, and lower costs for both the business and the wearer.
At the end of the day, the measurement methods of yesterday carry more obstacles and expenses than are necessary to bear. Whether it is time, money, or human assets, manual one-by-one measuring drains company resources. Providing employees with an accurate and remote method of measurement will help uniform manufacturers and suppliers save time, eliminate human error, reduce costs, and expand the reach of their businesses.
At 3DLOOK we have built a body data platform that enables a simple exchange of measurement and shape data between your business and your customers.
Want to learn more? Feel free to contact us here, we would love to hear from you.